硅胶产品硫化不充分不仅会导致硬度不足,还会引发一系列严重的性能缺陷和安全隐患,具体后果如下:
一、机械性能显著下降
弹性与回弹力降低
硫化不足的硅胶分子交联密度低,弹性模量下降,表现为制品易永久变形(如密封圈压缩后无法复原)。
拉伸强度与耐磨性减弱
未充分交联的硅胶拉伸强度可能下降30%~50%,耐磨性降低,易开裂或撕裂(如硅胶按键频繁按压后断裂)。
抗撕裂性差
硫化不完全的区域会成为应力集中点,制品在受力时易从薄弱处撕裂。
二、化学稳定性受损
耐高温性能下降
未充分硫化的硅胶在高温(>150℃)下易软化甚至分解,导致尺寸变形或功能失效(如高温密封件泄漏)。
耐老化性差
残留的未反应硫化剂和低分子链段会加速氧化,制品在紫外线和臭氧环境下易变脆、粉化(如户外硅胶件龟裂)。
耐化学腐蚀性减弱
对油类、溶剂等的耐受性降低,接触后可能溶胀或溶解(如工业油封失效)。
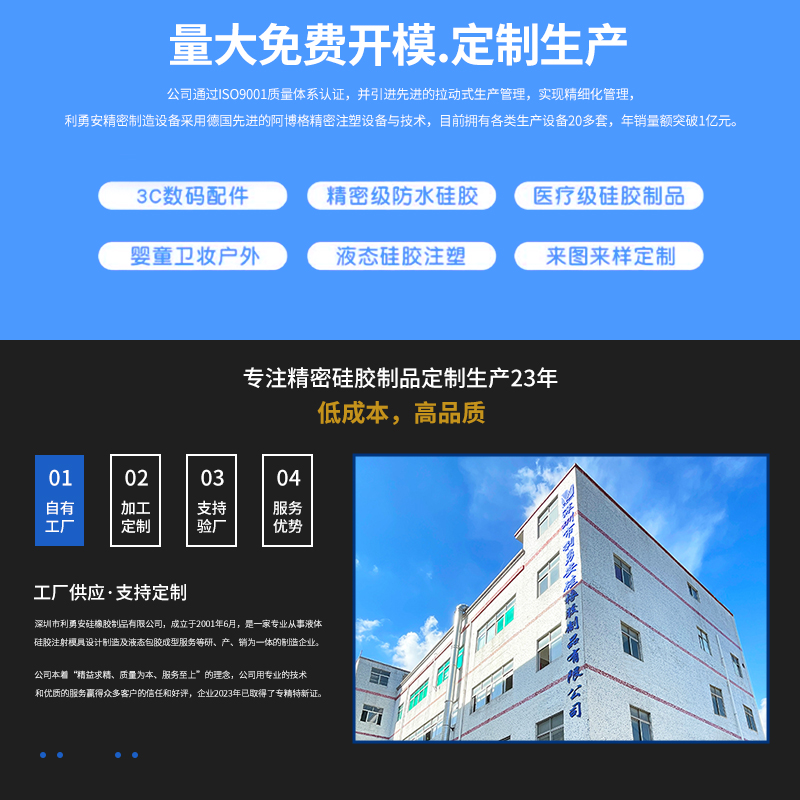
三、表面与功能缺陷
表面发粘或喷霜
未反应的硫化剂或低分子物质迁移至表面,导致粘手或白色粉末析出(喷霜),影响外观和触感。
易吸附灰尘和污染物
表面粘性增加会吸附环境中的颗粒物,降低洁净度(如医疗导管污染风险升高)。
气泡与内部缺陷
硫化不充分可能导致气泡残留,降低制品致密性,影响密封或绝缘性能(如电子灌封胶漏电)。
四、安全与合规风险
有毒物质释放
残留的硫化剂(如过氧化物)或未反应单体可能析出,不符合医疗或食品级认证(如FDA、LFGB)。
生物相容性不达标
医疗植入物若硫化不完全,可能引发人体排异反应或炎症(如乳房假体包膜挛缩)。
使用寿命缩短
制品在长期使用中因性能衰退导致提前失效,增加售后索赔风险(如汽车密封件早期泄漏)。
五、硫化不充分的常见原因
工艺参数不当:硫化温度过低、时间不足或压力不稳定;
配方问题:硫化剂添加量不足或分散不均;
模具设计缺陷:传热不均导致局部硫化滞后;
原材料异常:硅胶原料过期或受潮影响活性。
解决方案建议
优化硫化工艺
通过DSC(差示扫描量热法)确定最佳硫化温度和时间;
采用分段升温(如先低温预硫化,再高温充分交联)。
加强过程监控
使用硫化仪(如MDR)实时监测交联度(扭矩曲线);
定期检测制品的交联密度(溶胀法或硬度测试)。
改进材料与模具
选择高效硫化体系(如铂金催化加成硫化);
优化模具加热系统(如增加模温均匀性的水路设计)。
总结:硫化不充分会从机械性能、化学稳定性、表面质量到安全性全方位损害硅胶制品质量。生产过程中需严格把控硫化工艺参数,并通过检测手段(如交联度测试)确保硫化完全,尤其在医疗、食品、汽车等高要求领域更需重视。
深圳市利勇安硅橡胶制品有限公司—专注液态硅胶制品精密技术研发24年,联系电话:134-2097-4883。